
Dan on No Tool Left Behind With The Help Of Homemade Shadow Boards.Dan on 3D Printed Concrete Beam Improves Sustainability.Low-Cost Nanopositioning Hack Chat 6 Comments
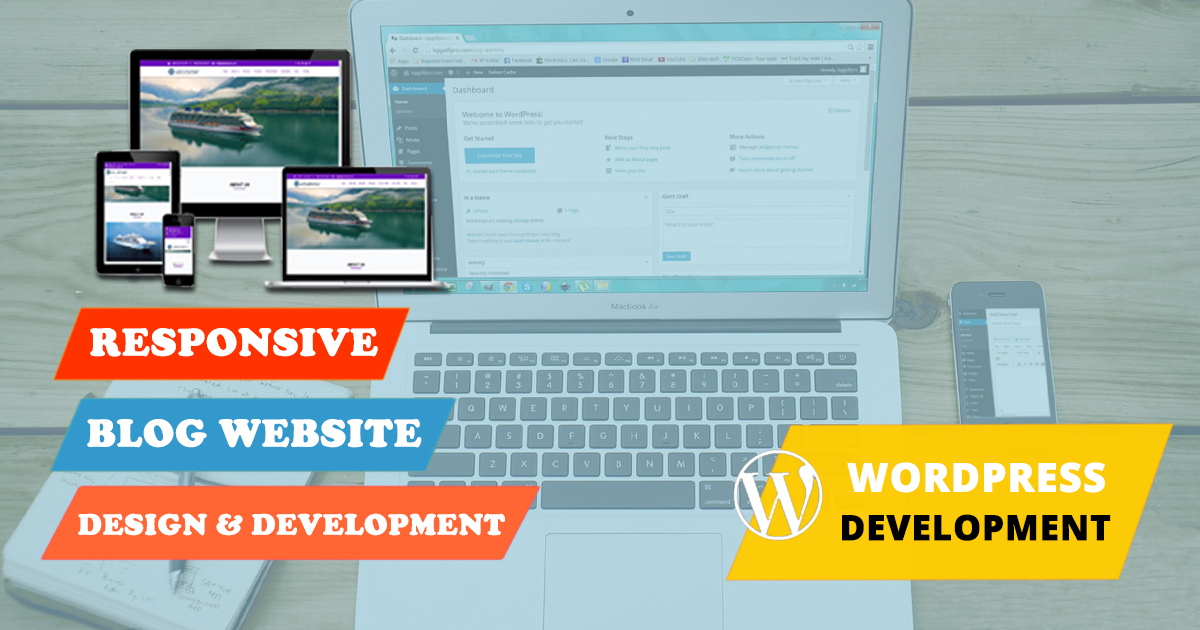
Rendering the toolpath onto the workpiece has everyday utility, and there are tons of other possibilities as well. But multiple contours is not even the most useful application. Tracing multiple contours becomes possible, by marking each with a tag, whereas with only one narrow-field camera, it’s not really feasible to scan the whole workspace. I am contemplating a dual-camera setup, with one wide-field that can capture the entire workspace with not too many pictures, and another narrow-field, high resolution camera, for more precise locations. Adjusting a segment of the toolpath should be possible in principle, but that is pretty advanced and that would be pretty challenging. This integration was the hardest part of the line follower, largely because I am still a novice at understanding how these plugins work.įor integrating a camera feed into the toolpath visualizer, I would think that should be doable, and definitely valuable for all the reasons you pointed out. The line follower operates within the gcode sender, so the movements work through the gcode sender, and not as a separate application. The line follower is an OctoPrint plugin, and OctoPrint is already a gcode sender of sorts. There is a lot of bang-for-the-buck to be had, where low-cost hardware can open whole worlds of functionality. The techniques that you and I are using are largely off-the-shelf existing techniques, but in the domain of CNC it is relatively uncommon. There are a lot of applications where imaging and computer vision can add a lot of value without particularly advanced technology. In some ways your application is entirely different, but I feel like it is in a similar spirit. Hi Tony, I think what you are showing has a lot of potential. Posted in cnc hacks Tagged gcode, Octoprint, opencv, path planning, webcam Post navigation Let us know in the comments if you’ve got some other good examples. We’ve seen a similar OpenCV approach used for center-finding bore holes, but while we’ve seen a few webcams used with laser cutters, the CNC mill applications seem largely untapped. Once you see the girl pirate robot that ’s daughter made, you’ll get the idea. This project is clearly an invitation to keep on hacking, an appetizer. But mounting a webcam to a CNC toolhead and using it for various pathing problems really opens up tons of possibilities: visual homing, workpiece edge finding, copying parts, custom fitting odd shapes, and more. Right now, it’s limited to paths with non-crossing lines, and probably with good contrast and a nice dark line - all the usual CV restrictions. The user can enter the usual milling parameters: speeds, feeds, depth of cut, tool offset, milling direction, etc. It starts off with a fiducial arrow for scale and orientation, then it mores the webcam around the scene.

Under the hood, OpenCV is doing a lot of the image processing, including line detection, and the iterative “find the line” and “move the toolhead” steps really show off what computer vision can do.
#Drawit wordpress code
The code is on GitHub and there’s a demo video embedded below. The plugin lets you skip the modeling step entirely, going straight from a CNC-mounted webcam that reads your scribbles and gives you a Gcode toolpath in return.
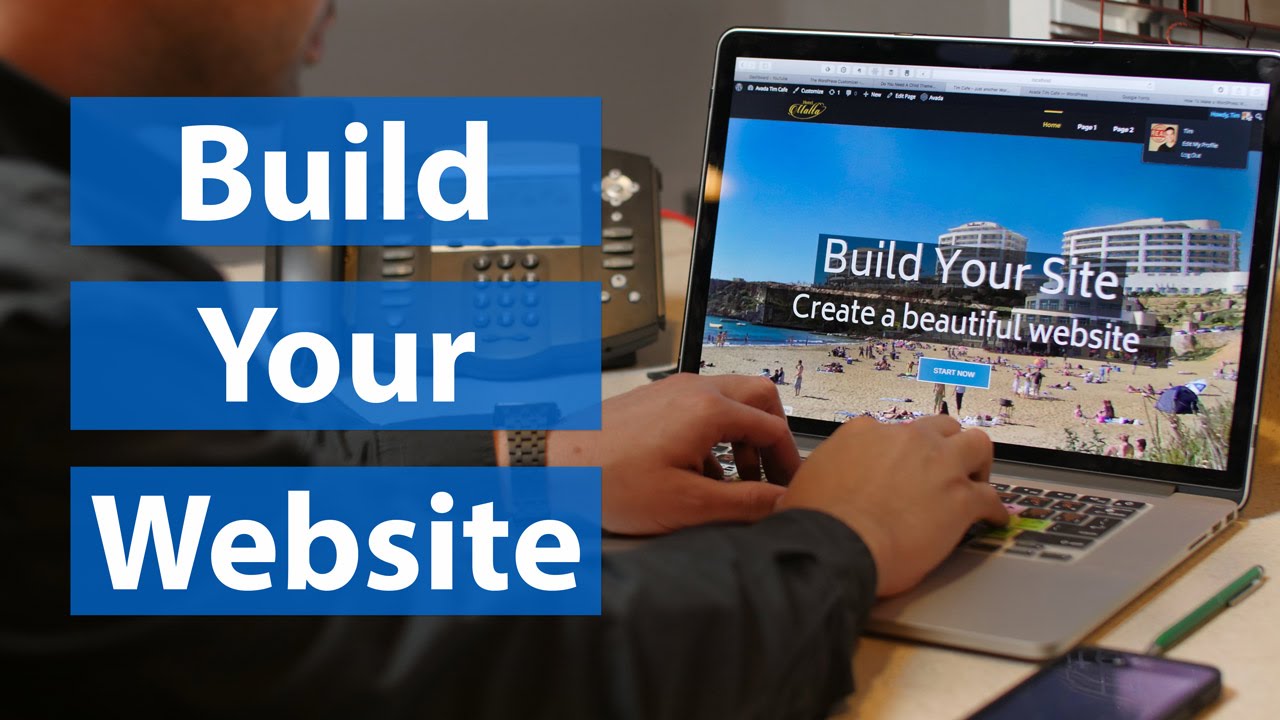
Aka hit us with a line-tracing plugin for OctoPrint that cuts out whatever 2D shape you draw on a piece of wood.
